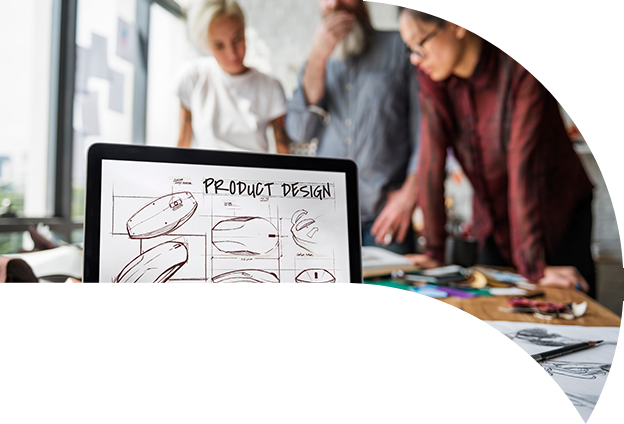
Solutions
Our Approach
Giving you intelligent technology tools to solve invisible problems.
Manufacturers in every sector are incorporating promising new processes and materials into product development and production—which often involve coating, sealing and bonding.
Because these molecular interactions are invisible, a host of unseen environmental conditions and unwitting human choices can compromise surface integrity during production, leading to costly flaws and breakdowns.
Brighton Science enables you to confidently assess surface readiness for bonding, coating or sealing at the point of preparation. Unlike systems that are limited to the lab, our tools collect and share data across processes and functions—giving you unprecedented visibility and insight to real-life adhesion, manufacturing, product development and supply chain challenges.
In short, our solution allows you to predict molecular interactions on your surfaces that affect bonding. We help you make sure things stick when you want – and don’t stick when you don’t.
Whether you are testing the bonding requirements for a new substrate in the lab or monitoring the efficacy of adhesion on an established production line, our tools provide you with the data you need to solve any immediate issue, prevent it from recurring and improve overall control of your processes.
With decentralized manufacturing on the rise and more people working remotely, having the ability to selectively share data with divisions, suppliers and teams around the world is more critical than ever.
So what’s going wrong?
Surface Intelligence in your hands
Networked Solutions
BConnect
We began by providing a unique measurement tool. Now we’ve combined that tool with next-generation connectivity, data and insights to give you an unprecedented level of surface intelligence that will change the way you think about—and work with—adhesion.
Non-Networked Solutions
Surface Analysts
The gold-standard measurement device that has helped hundreds of companies solve surface readiness problems throughout their manufacturing environment.
Solve, prevent, control: Surfaces, meet technology.
We began by providing a unique measurement tool. Now we’ve combined that tool with next-generation connectivity, data and insights to give you an unprecedented level of surface intelligence that will change the way you think about—and work with–adhesion.
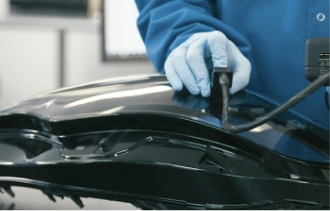
Immediate Needs
Adhesion issues can arise at any time in the manufacturing process. We’ll partner with you to quickly solve the problem—and prevent it from ever happening again.
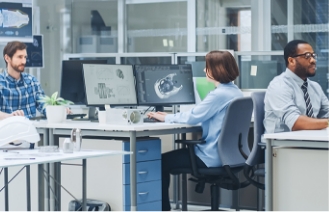
Product Development
Want to unleash innovation and increase your odds of a timely, successful product launch? We partner proactively with product development teams to ensure foolproof adhesion—minimizing delays and recalls.
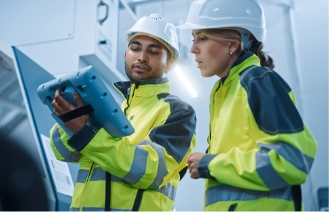
Operational Excellence
Get end-to-end visibility and process control— no matter if your teams are local or spread across the globe.
Connect with Brighton Science
Talk to an Expert
Our team has decades of specialized expertise across key industries, enabling us to quickly assess how we can best support you. We make thoughtful recommendations on how to integrate surface intelligence tools and technology into your operations over time—beyond just a single device or a quick fix.
Brighton Science is
the global leader
in surface intelligence.
Tell us your goals or challenges, and we can advise you on specific solutions you can put to work immediately or build into your optimization processes.
What could this mean for you?
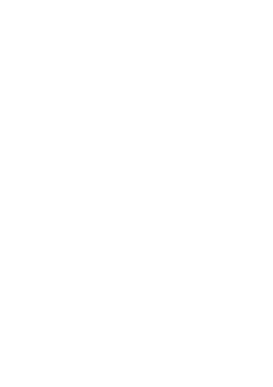